Sticky sand
- According to the formation mechanism, sand sticking can be divided into mechanical sand sticking and chemical sand sticking. The metal on the surface of the casting is oxidized, and the oxide reacts with the molding material to form low melting point compounds. During pouring, the pressure of molten metal is too large to penetrate the sand gap; When the temperature of molten metal is too high and it remains liquid in the sand mold for a long time, the ability of molten metal to penetrate the molding sand is strong, and it is easy to have a chemical reaction with the molding material, resulting in sand sticking; The fire resistance of molding materials is low.
- Prevention methods. On the premise of ensuring sufficient air permeability, raw sand with fine particle size shall be selected as far as possible for wet molding; Improve the compactness of sand mold, especially the compactness of the lower part of tall sand mold; Pulverized coal, heavy oil and asphalt can be added to the green sand of cast iron; Properly reduce the pouring temperature; Reduce the sand consumption to improve the cooling rate of the sticky sand layer; Avoid local overheating of mold and core; Choose molding materials with high fire resistance or strong cooling capacity.
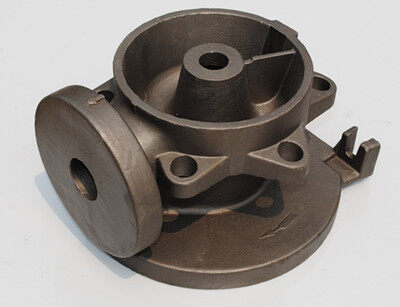
Slag inclusion
- Before pouring, the scum on the molten metal was not cleaned, the slag was not well blocked during pouring, and the scum entered the mold with the molten metal; The design of the pouring system is unreasonable, and the slag blocking effect is poor. The slag entering the pouring system directly enters the mold cavity without being discharged.
- Prevention methods. The pouring system should make the liquid metal flow smoothly, and set up slag collecting bags and slag retaining devices; Try to reduce the content of sulfur in molten metal; Try to increase the discharge temperature of molten metal; The ladle should be kept clean, and it is best to use teapot ladle; Slag removers such as straw ash and cryolite can be added before pouring.
Sand washing, sand hole, and sand falling
- The strength of sand mold and sand core is low, and the mold and core are excessively baked; The flow rate of molten metal is too fast, and the local surface of the core is scoured for too long; The parting surface is uneven and the core head gap is small; During the operation of core lowering and mold closing, the mold and core are partially crushed, impacted and collided in the process of fastening the mold, and the mold and core are partially desanded; The moisture content of molding sand is too high and the permeability is poor, and boiling occurs during pouring; The scattered sand in the sand mold was not cleaned up, resulting in sand holes formed by loose sand.
- Prevention methods. Improve the strength of the mold and core; Prevent excessive baking of mold and core; Prevent the ingate from facing the mold wall or corner; Specially configured erosion resistant and refractory products shall be used for parts strongly scoured by molten metal; For large dry type, the appropriate negative parting number should be reserved; In the process of mold closing, mold fastening, pressure iron releasing and transportation, the operation of molding sand should be careful to prevent impact and collision; Reinforcement measures (such as inserting nails) shall be taken at the repaired part and weak part of the mold and core; Carefully check and remove the excess sand before lowering the core and closing the box.
We are a cast iron steel, cast iron foundry near me, cast iron pulley exporter supplier wholesaler, our products satisfy our customers. And we want to be your long-term partner, any interests, welcome to contact us.